Customers bring many questions to our team about their wire cable harnesses. This question is about how customers are experiencing high resistance when mating connectors. One of the potential causes of an electrical connection failure is unwanted/unknown levels of contact resistance.
While there are many variables but here are a couple common occurrences and with potential solutions the Custom Interface team want to share with you:
Occurrence :
Wires were specified to be twisted within a short distance from where they exit the connector, which puts pressure on the terminals as they are twisted within the housing.
With certain connectors, terminals can float slightly within the housing, and any directional load applied can twist or shift them in a way that can cause issues, such as:
-
- Increased mating resistance which can dislodge terminals or prevent mating all together.
- Reduced terminal retention force if the locking tab features are not fully engaged.
Solution:
Manufacturer's documentation specifies: Keep twists a minimum of 0.75" away from the back of the connector to allow wires to exit flat and straight, and not put stress on the terminals.
Example:
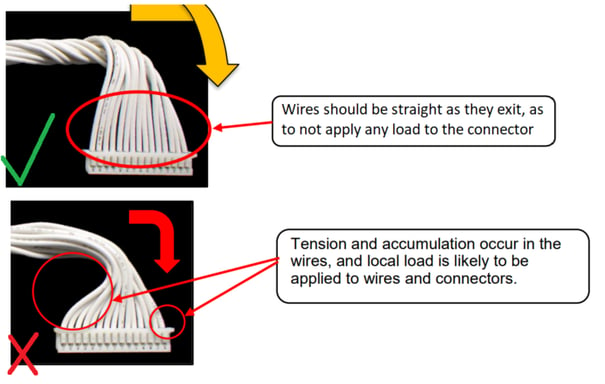
Occurrence :
Terminals were not secured well by the housing, making the connector potted and locked into a bad orientation.
Solution:
Mate the connector before and during potting until cured, therefore ensuring proper orientation of the terminals.
Example:
Applying Epoxy to the backside of the connector can eliminate the possibility of dislodging terminals, however this can also cement-in certain pre-existing defects.
In the example below, twists were performed too close to the connector, which forced the terminals enough to prevent mating the connectors entirely. This was discovered after epoxy was applied, and thus the cable was scrapped.
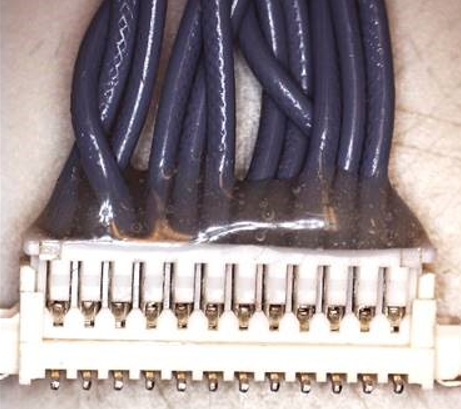
Best Practice:
Specifying a minimum distance between the connector and any twists, ties, heat shrink, or other bundling method as shown below is one of the best ways to ensure proper mating.
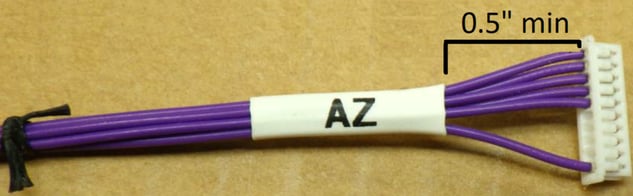
We are very proud of our team who makes every effort to adapt to the constant changes to meet the highest wire harness manufacturing standards. From the point of design and assembly at the drawing board to the finished wire harness, our team goes through the step-by-step planning process. Each wire harness has a specific purpose and usually integrates into a larger electronic network. They understand that wire harnesses are indispensable and looking forward to building yours.
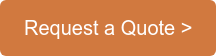
Do you have a problem that is puzzling to your team?
Please share as a comment below. Our team would be happy to offer suggestions.
Leave a Comment